Professional Experience
FutureSearch: AI Research Engineer (2025 to Present)
FutureSearch is a startup leveraging AI to answer tough questions, including market research and forecasting the future. I joined as an AI Research Engineer in 2025.
Formlabs: Systems Integration Engineer (2015 to Present)
Based in Somerville, Massachusetts, Formlabs designs professional-grade 3D printers. Unlike most 3D printers which extrude filament through a heated nozzle (fused deposition modeling or FDM), Formlabs printers use light to solidify either liquid resin (stereolithography or SLA) or plastic particles (selective laser sintering or SLS) into complex objects. These optical techniques can provide better surface finish, finer detail and superior mechanical properties compared to FDM.
We were the first to bring stereolithography to the desktop with the Form 1. Since then, with the release of the Form 2, 3 and 4, we have become the all-time top seller of professional 3D printers.
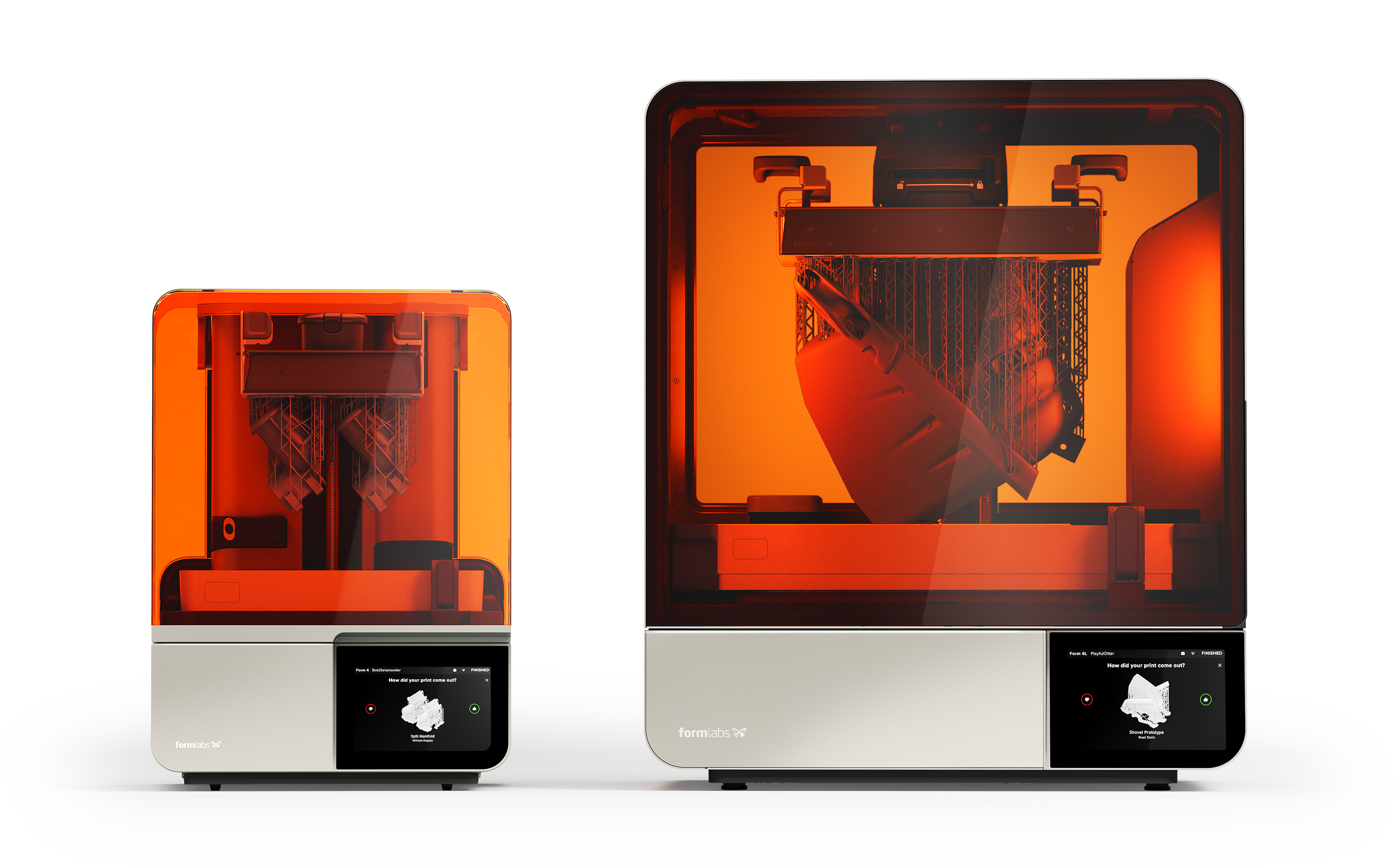
I work on the Systems Integration team, which operates at the intersection of mechanical, electrical and software engineering. We are responsible for assembling the printer’s many subsystems into a reliable, well-oiled machine. The team is highly interdisciplinary, taking on different responsibilities during the product’s development cycle.
During the early stages, we design and prototype new subsystems to determine what the final product will look like. This requires close collaboration with other engineering teams, from hardware to software. Early in the Form 4 prototype phase, I was the lead architect and developer of the core firmware application for running 3D prints. Written in Python, the application had to precisely move motors and time UV exposure to successfully produce parts. It also needed to monitor a myriad of sensors to maintain a suitable printing environment, as well as log data to answer key questions about the new hardware design. And it had to be easily extensible so that new features could be quickly added in response to the needs of the project.
As the new printer moves towards production, the Systems Integration team focuses on maximizing reliability to deliver the best experience to our users. I designed a system to robustly manage the data stored on the Form 4’s user-replaceable components, such as the resin tank and cartridge. This system needed to gracefully handle read and write failures, since the communication protocol was noisy and the user could remove the component at any time. It had to perform exhaustive security and validation checks to protect Formlabs’ primary revenue stream from counterfeits. And it needed to be easily extendible to other data formats and storage media.
Our work doesn’t stop once printers have made their way into customers’ hands. We listen to feedback from our users and continue to make improvements that can be deployed via software updates. For instance, not long after shipping the Form 3, we uncovered an issue with the its resin level sensor. Even though it only affected a small proportion of printers, those who were impacted had a risk of their prints failing due to lack of resin. To avoid returning the printers for repair, which would have inconvenienced our customers and cost us money, I developed a firmware solution that saved both time for our users and money for Formlabs.
Every year, Formlabs runs a hackathon for all employees. You can read about a few of the fun projects I’ve worked on.